Inventory Picklists
With our Industry-Leading Inventory software’s picklist feature, picklists can be created directly on our system. Picklists are created with the barcoded items that need to be retrieved from storage and sent to warehouse pickers to fulfill an order. Once the picklist is generated within the system, the order fulfillment and picking processes can begin.
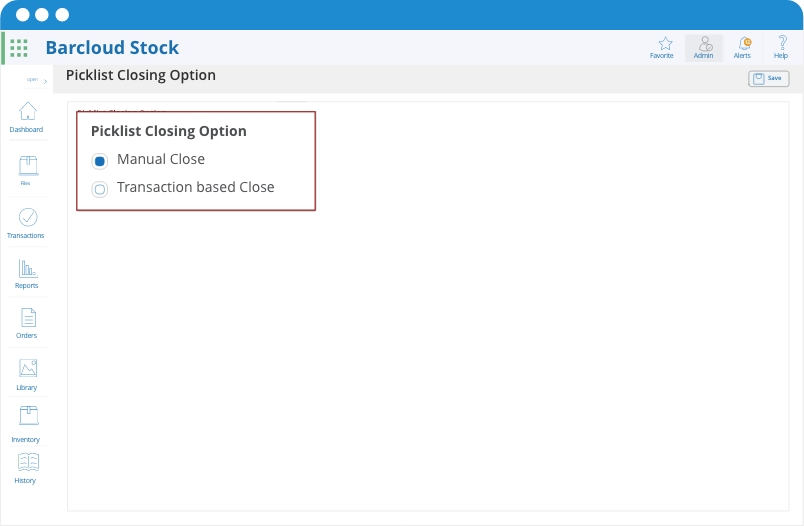
Picklist Configuration Settings
Users can adjust/configure the “Picklist Closing Options” when preparing the picking process. This configuration setting lets users choose if they would rather manually close the pick list (“Manual Close”) or automatically close the picklist (“Transaction Based Close”). Once the inventory items have been picked, they can proceed with the order fulfillment process and finally move on to Pack and Ship their inventory pick.
Picklist Reporting
With our inventory picklist reporting feature, users can fully configure each report and picklist to reflect the information that is the most important to their organization’s needs. They can decide what information is displayed in the reports such as specific locations to pick from, images and part numbers, quantities, etc.