PICA Manufacturing Solutions
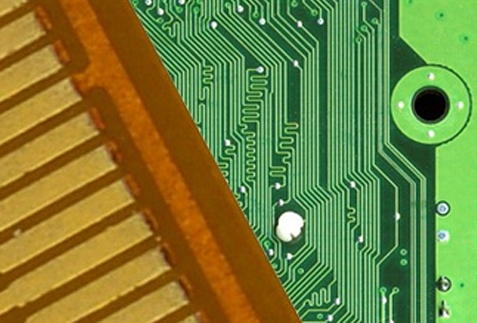
SUMMARY
PICA Manufacturing Solutions specializes in the design, manufacturing and assembly of printed circuit boards. The company needed an automated inventory management system that integrated with QuickBooks Enterprise Solutions and enabled employees and management to easily track hundreds of parts in real time as they moved from vendors through manufacturing, production and assembly in PICA’s multiple locations.
THE CHALLENGES
As a manufacturer and assembler of printed circuit boards, PICA faces unique industry challenges. The company does a lot of assembly work that involves many moving parts such as hundreds of different components, multiple locations and multiple outside companies that are part of PICA’s manufacturing, production and assembly processes.
The company needs to give its employees real time knowledge of where parts are at any time, where inventory levels stand at various locations and how parts are moving throughout the company, whether they’re coming in from a vendor, the warehouse, or some other location. Having this level of knowledge and awareness about its inventory helps PICA improve the efficiency of its supply chain and ensure assembly is not held up due to missing parts or the delayed delivery of parts at various locations. ASAP Systems’ inventory tracking solution gives PICA this level of awareness. In addition, it gives employees and management the ability to share that information by easily creating custom reports that can be exported into common file types (PDF, Excel and Word for example) and emailed. These reports help management to more accurately forecast and more efficiently coordinate purchasing — creating a more lean supply chain for the company.
FITTING THEIR NEEDS
The process of production, manufacturing and assembly for printed circuit board electronics involves many moving parts and multiple stages that often involve different locations and numerous companies. To smoothly transition between stages, companies need real–time information and updates on inventory counts at any one location, as well as information on how parts are moving throughout the entire system. PICA, for example, tracks hundreds of individual electronic components and other parts that are used in assembly, most of which are drop shipped directly to customers where they are then assembled into a printed circuit board. Many of these never pass through PICA’s main warehouse. The ones that do make it into the warehouse tend to be components in PICA’s most complicated assemblies. In this case, they are kitted in the warehouse before they are shipped to another location.
PICA was using QuickBooks to track the movement of its parts. Though a leader in business accounting software, QuickBooks does not handle inventory management effectively.
“QuickBooks is great for accounting, but it just doesn’t handle assemblies well,” said Justin Shevelow, a PICA Systems manager. “It was difficult for us to track the movement of parts from the stockroom in real time.”
Shevelow started looking for specialized inventory management software. It had to: 1) integrate with QuickBooks, 2) be highly accurate and responsive, 3) track and report on the movement of PICAs parts in real time at multiple locations, 4) be intuitive and easy to use and 5) serve PICA’s unique needs with regard to kit assembly.
Most importantly, the software needed to give PICA management and employees access to stock/inventory information in real time, which is key to PICA building more efficiency into its manufacturing and assembly process at its worldwide locations.
THE SOLUTION
“This software is helping us better understand our inventory and saving time on counts,” said Shevelow. “We are now, we’re more efficient because we have greater awareness of the status of our inventory throughout the company, regardless of location.”
ASAP Systems’ engineers worked with PICA to determine what the company’s unique needs were. ASAP Systems Inventory System then recommended it’s client server software for inventory management and tracking plus the “kitting” module which gave PICA the additional features they needed. PICA also purchased a Motorola handheld scanner that reads barcoding and a barcode printer so employees could scan and update inventory directly in the stockroom.
“ASAP System’s price was very reasonable for everything the software can do,” said Shevelow. “And during the installation process, their support was extremely professional and helpful. For example, we use an off–site cloud server to host our QuickBooks application and getting them to host this additional software was a challenge, but ASAP helped us through that.”