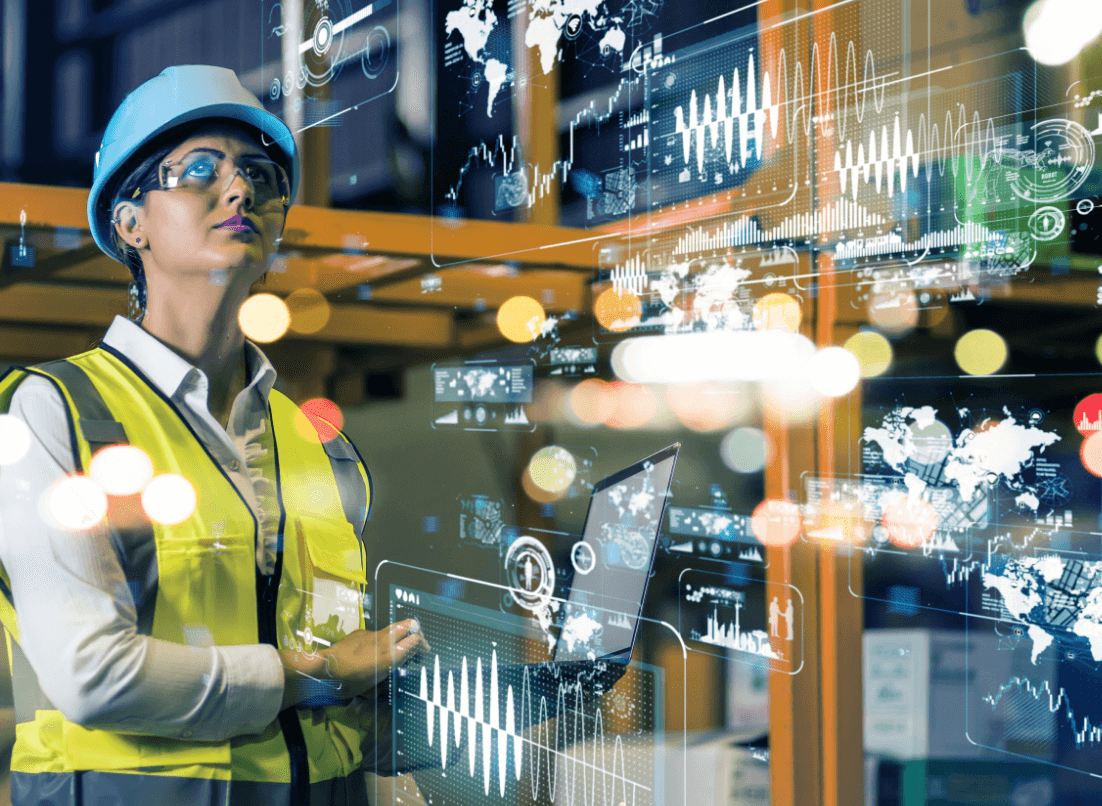
What is an Inventory Management System?
An inventory management system is a tool or set of tools that help businesses track and manage their inventory levels, orders, sales, and deliveries. It serves as the backbone for businesses to monitor stock quantities, maintain optimal inventory levels, and manage supply chain operations. The system can range from simple spreadsheets to sophisticated software solutions, and it typically includes features such as:
Effective inventory management systems help businesses reduce costs, improve customer satisfaction by ensuring products are in stock, and increase operational efficiencies by automating many manual tasks. They are essential in manufacturing, warehousing, healthcare, education, and any other industry that involves stock control. Our Inventory System can be used by any business regardless of company size or industry.
You Can Learn More About Our Inventory System and its Features Here -> https://asapsystems.com/products/inventory-system/
https://asapsystems.com/products/inventory-system/system-features/
How does an Inventory Management System work?
An Inventory Management System works by tracking and managing the flow of goods from procurement to sales, ensuring that inventory is maintained efficiently throughout the supply chain. Here’s a detailed look at how these systems typically function:
Overall, an Inventory Management System automates and optimizes the process of tracking and managing inventory, ensuring that businesses can operate more efficiently and effectively. This automation not only helps in reducing human error but also enhances the ability to scale operations and respond quickly to market changes.
You Can Learn More About Our Inventory Management System Here -> https://asapsystems.com/products/inventory-system/
Inventory Management System Examples
Inventory management solutions vary widely in complexity and format. At one end of the spectrum, there are basic methods such as manual record-keeping with pen and paper or spreadsheets, which require manual input of data. At the other end, there are advanced software solutions designed to automate a significant portion of the inventory management tasks. Here’s a more detailed exploration of the spectrum of inventory management solutions:
1- Manual Record-Keeping
Pen and Paper:
- Description: This basic approach uses physical ledgers or notebooks for inventory recording.
- Use Cases: Best suited for very small businesses with minimal inventory and low transaction volumes.
- Features: Simple, no-cost setup; no need for technical infrastructure.
- Limitations: Prone to errors, not scalable, and time-consuming to maintain and search.
2- Standalone Systems
Standalone Inventory Management Software:
- Description: Software designed to manage inventory at a single location without the need for broader integration with other business systems.
- Use Cases: Ideal for small businesses operating from a single site, such as independent small warehouses.
- Features: Basic functionality like stock level tracking, order management, and simple reporting.
- Limitations: Limited integration capabilities, which might require manual updates between systems.
You Can Learn More About Our Standalone System Here -> https://asapsystems.com/customers/standalone-system/inventory/
3- Multisite Systems
Multisite Inventory Management Software:
- Description: Systems designed to manage inventory across multiple locations.
- Use Cases: Fits small to medium-sized companies managing inventory across several sites, such as franchise operations or businesses with several branches.
- Features: Centralized control over inventory, ability to view and transfer stock between locations, and consolidated reporting.
- Limitations: More complex to implement and manage than standalone systems.
You Can Learn More About Our Multisite System Here -> https://asapsystems.com/customers/business-multisites/inventory/
4- Enterprise Systems
Enterprise Resource Planning (ERP) Systems:
- Description: Comprehensive systems that integrate all facets of a business’s operations, including inventory across multiple sites and systems.
- Use Cases: Suitable for large corporations that need robust functionality to oversee complex and extensive operations.
- Features: Advanced inventory forecasting, automation of supply chain processes, integration with financial and HR systems, and detailed analytics.
- Limitations: High cost, significant implementation time, and complexity.
You Can Learn More About Our Enterprise System Here -> https://asapsystems.com/customers/enterprise-solution/
5- Cloud-Based Systems
Cloud-Based Inventory Management:
- Description: Inventory systems hosted on the cloud, providing accessibility from any location with internet access.
- Use Cases: Ideal for businesses of any size that value ease of access, scalability, and reduced IT overhead.
- Features: Real-time data updates, scalability, backup and disaster recovery, and lower upfront costs.
- Limitations: Dependence on internet access and potential concerns over data security.
You Can Learn More About Our Cloud-Based System Here -> https://asapsystems.com/products/cloud-based/
6- On-Premise Systems
On-Premise Inventory Management Systems:
- Description: Systems installed and run on a company’s own servers and infrastructure.
- Use Cases: Best for organizations that require full control over their data and infrastructure, such as those with stringent security requirements or without reliable internet access.
- Features: Complete control over the system and data, typically more customizable.
- Limitations: Higher upfront costs for hardware and software, ongoing maintenance required, and scalability can be costly and complex.
You Can Learn More About Our On-Premise System Here -> https://asapsystems.com/products/on-premise/
Each type of inventory management system offers distinct advantages and poses specific challenges, making it crucial for businesses to choose a solution that aligns with their operational needs and growth objectives.
You Can Learn More About Our Inventory Management System Here -> https://asapsystems.com/products/inventory-system/
How long does it take to implement an inventory management system?
The time required to implement an inventory management system varies significantly based on several key factors. For smaller businesses, implementation might take a few weeks to a few months, leveraging simpler systems and smaller catalogs. In contrast, larger enterprises might require several months to over a year, especially if the system is complex, requires customizations, or needs to be integrated with existing software like ERP or CRM systems.
Additional factors that influence the timeline include the extent of data migration needed, the training required for staff, and the necessary testing and troubleshooting to ensure the system operates smoothly. Generally, one can expect a straightforward system setup to take 1-3 months, while more involved installations could stretch to 6 months or more, depending on the organization’s size and specific needs.
How much does an Inventory Management System cost?
An inventory system’s price can differ greatly depending on the organization’s size and specific needs. Ideal software providers typically offer a range of inventory systems at different price levels to suit the size and requirements of your organization.
To provide a clearer picture of the varying costs, we will guide you through a 4-level pyramid that showcases the different inventory systems we provide for various organizations, each with its associated costs:
When to Upgrade your Inventory Management System?
What is Automated Inventory Management?
Automated inventory management uses digital systems (software) to control and optimize stock levels. This contrasts with manual methods where stock is tracked by hand or through physical counting.
How It Works
- Digital Twin: The software creates a virtual representation of your physical inventory.
- Tracking: Barcode scanners or integrations with various systems track stock arrivals and sales, updating the digital record in real time.
- Internal Movements:Transfers between warehouses or locations into products are also recorded within the system.
- Order Management: Purchase orders for restocking and sales orders for fulfilling customer demand are handled through the software.
1- Manual System
- Tracking: Manual updates to spreadsheets or lists; physical counts for stock checks.
- Accuracy: Prone to human error.
- Cost: Low initial cost; potentially high labor costs for larger inventories.
- Suitability: Best for very small businesses with simple inventory needs.
2- Automated System
- Tracking: Real-time updates through barcodes, integration, etc.
- Accuracy: More accurate due to automation.
- Cost: Higher software investment; potential for long-term savings in labor and errors.
- Suitability: Ideal for growing businesses or those with complex inventory.
- Additional Benefits: Automated reordering, detailed reports, integration with other systems.
You Can Learn More About Our Cloud-Based System Here -> https://asapsystems.com/blog/inventory-asset-tracking-blog0042/
Benefits of Automated Inventory Management: A Comprehensive Guide
Automated inventory management systems offer numerous advantages that empower businesses to optimize operations, reduce costs, and drive growth. Here’s a consolidated overview:
You Can Learn More About Our Cloud-Based System Here -> https://asapsystems.com/blog/inventory-asset-tracking-blog0059/
Periodic vs. Perpetual Inventory Management Systems: Choose the Best Fit for Your Business
Choosing the right inventory system is crucial for businesses of all sizes. We offer innovative software solutions that address the drawbacks of both periodic and perpetual systems, empowering you to make an informed decision.
1- Periodic Inventory System
A periodic inventory system involves physically counting your inventory at scheduled intervals. Historically, this method has been favored for its simplicity and lower upfront costs, making it accessible for businesses with limited resources. However, it traditionally lacks real-time visibility and can be prone to inaccuracies between counts.Our software solution transforms the periodic system by:
2- Perpetual Inventory System
A perpetual inventory system continuously tracks inventory levels in real-time using software and technology like barcode scanners. This method offers superior accuracy and insights, but it has traditionally required a larger investment in software and hardware. Our software solution enhances the perpetual system by:
Which System is Right for You?
The best inventory system for your business depends on your unique needs and priorities. Consider the following factors:
- Business size and complexity: A periodic system might suffice for smaller operations, while growing businesses may benefit from the detailed insights of a perpetual system.
- Product types: Perishable or high-demand items necessitate the real-time tracking of a perpetual system.
- Budget:Evaluate the upfront and ongoing costs of each system, considering our affordable software solutions.
- Technology comfort level: Choose a system that aligns with your team’s technical skills and preferences.
With our innovative software, both periodic and perpetual inventory systems become powerful tools for managing your stock effectively. Explore our solutions and discover how we can help you optimize your inventory management, regardless of your chosen method.
Check out all the features you can select here -> https://asapsystems.com/products/inventory-system/system-features/
Mastering Inventory Management: Essential Techniques for Business Success
Effective inventory management is essential for any business that deals with physical goods. Whether you’re a small company or a large enterprise, implementing the right inventory management techniques can significantly impact your bottom line. Let’s delve into the most common and effective methods:
1- Inventory Costing Methods
- FIFO (First-In, First-Out): This method assumes that the oldest inventory is sold first. It’s ideal for perishable goods or items with fluctuating prices.
- LIFO (Last-In, First-Out): The newest inventory is sold first under LIFO. This method may be advantageous for tax purposes in certain situations.
2- Inventory Control Methods
- Just-in-Time (JIT): With JIT, inventory is ordered and received only as needed, minimizing holding costs. However, it requires a reliable supply chain to prevent stockouts.
- Just-in-Case (JIC): JIC involves holding safety stock to buffer against unexpected demand or supply chain disruptions. While it offers protection, it can tie up capital.
- ABC Analysis: This method classifies inventory into three categories (A, B, and C) based on value and importance, allowing you to prioritize management efforts.
3- Demand Forecasting and Planning
- Demand Forecasting:Predicting future customer demand helps optimize inventory levels, preventing both overstocking and stockouts.
- Economic Order Quantity (EOQ): This formula calculates the optimal order quantity to minimize total inventory costs.
- Reorder Point: This is the inventory level at which a new order should be placed to avoid stockouts.
4- Other Techniques
- Dropshipping:Outsource inventory storage and fulfillment to a third-party supplier.
- Cross-docking: Receive and immediately ship goods without storing them in a warehouse.
- Cycle Counting: Regularly count a small portion of inventory to maintain accuracy and identify discrepancies.
5- Choosing the Right Technique
The most suitable inventory management technique for your business will depend on factors like your industry, product type, sales volume, and supply chain complexity. By understanding the various methods available and their pros and cons, you can make informed decisions to optimize your inventory management and ultimately drive business success.
The Importance of Creating an Ecosystem for your operations -> https://asapsystems.com/blog/inventory-asset-tracking-blog0031/
Barcodes vs QR Codes for inventory tracking: the differences
While both barcodes and QR codes are valuable tools for inventory tracking, they have distinct differences that make each better suited for specific scenarios. This table outlines their key features and considerations to help you choose the right solution for your inventory management needs:
1-Barcodes
- Data Capacity:Limited (usually a few dozen characters).
- Data Types:Primarily numeric data (e.g., SKU numbers).
- Scanning:Requires a dedicated barcode scanner.
- Error Correction:Limited.
- Versatility:Best for basic inventory tracking and product identification.
- Cost:Lower cost to implement due to simpler technology.
2-QR Codes
- Data Capacity:High (up to thousands of characters or bytes).
- Data Types:Numeric, alphanumeric, URLs, contact information, images, etc.
- Scanning:Can be scanned using smartphones and tablets.
- Error Correction:Higher levels of error correction, readable even when partially damaged.
- Versatility:More versatile, can store additional product information, track maintenance history, link to URLs.
- Cost:Slightly higher cost due to more complex technology.
Click Here To See How Our Barcode Tracking Can Transform Your Operations -> https://asapsystems.com/blog/inventory-asset-tracking-blog0034/
What is the role of barcodes in inventory management?
Barcodes are a fundamental tool in modern inventory management, revolutionizing how businesses track and manage their stock. By assigning a unique code to each item, barcodes enable quick and accurate identification, significantly streamlining various warehouse processes.
Adopting barcodes in inventory management is a proactive step towards improving efficiency, accuracy, and profitability. Barcodes are versatile and can be tailored to various industries and business sizes, making them an invaluable asset for modern warehouses, distribution centers, and production firms.
Inventory Systems: Worth the Money to Save Money -> https://asapsystems.com/blog/inventory-asset-tracking-blog0020/
Cloud-Based vs. On-Premise Inventory Management Software: Which is Right for Your Business?
Adopting barcodes in inventory management is a proactive step towards improving efficiency, accuracy, and profitability. Barcodes are versatile and can be tailored to various industries and business sizes, making them an invaluable asset for modern warehouses, distribution centers, and production firms.
1- Cloud-Based Inventory Management with Us
Pros:
- Accessibility: Access inventory data from anywhere with an internet connection, ideal for businesses with multiple locations or remote teams.
- Cost-Effectiveness:Our inventory solution involves lower upfront costs with a subscription-based model, eliminating the need for expensive hardware and maintenance.
- Scalability: Easily add or remove users and features as your business grows.
- Automatic Updates:Receive the latest software features and security patches without manual intervention.
Cons:
- Data Security Concerns? Our cutting-edge inventory system prioritizes your data security with robust measures and industry best practices.
- Limited Configuration?Our software offers flexible configurable options to tailor the solution to your unique workflows.
- Internet Dependency Worries? We provide offline capabilities and ensure a seamless experience even with intermittent connectivity.
2- On-Premise Inventory Management
Pros:
- Data Control: Complete control over data security and storage, ideal for businesses with strict compliance requirements.
- Configuration:Greater flexibility to tailor the software to your specific needs.
- Offline Access:Can be accessed without an internet connection, suitable for businesses with unreliable internet access.
Cons:
- High Upfront Investment: Requires a significant initial investment in software licenses, hardware, and IT infrastructure. Our cloud-based solution offers a cost-effective alternative with predictable subscription pricing.
- Maintenance Overhead:Requires dedicated IT personnel for updates, maintenance, and troubleshooting. With our inventory system, maintenance and updates are handled seamlessly, freeing up your IT resources.
- Limited Accessibility: Access to inventory data is restricted to on-site users. Our software enables access from anywhere, enhancing collaboration and decision-making.
3- Choosing the Right Solution
To make an informed decision, carefully evaluate your business needs and priorities. Consider the following factors:
- Budget: Assess your financial resources and determine whether you prefer lower upfront costs (cloud-based) or higher initial investment (on-premise).
- Accessibility:Determine if you need remote access to inventory data or if on-site access is sufficient.
- Data Security: Evaluate the sensitivity of your inventory data and decide if you need complete control over security measures. We offer robust security features to safeguard your data.
- Configurable: Determine if you require extensive various options to align the software with your unique business processes. We provide flexible configurations to homeset your specific needs.
- Scalability: Consider your growth plans and choose a solution that can easily adapt to your changing needs. Our software is designed to scale seamlessly with your business.
4- Don’t Hesitate to Reach Out
If you are unsure which option is best for your business, reach out to our expert team for a personalized consultation. We can assess your specific requirements and recommend a solution that aligns with your goals and budget.
Learn more about our Cloud-Hosted Inventory System Here -> https://asapsystems.com/products/cloud-based/
Learn more about our On-Premise Inventory System Here -> https://asapsystems.com/products/on-premise/
Need help? Contact us through here -> https://asapsystems.com/company/barcloud-contact-us/
Minimize Inventory Risk, Maximize Profits: The Power of Modern Software
Traditional inventory management is riddled with risks like inaccurate forecasts and outdated stock, leading to lost profits and missed opportunities. But there’s a solution: inventory management software. This powerful tool mitigates those risks, optimizes your inventory, and boosts your bottom line.
How to Choose the Best Inventory System -> https://asapsystems.com/blog/choose-the-best-inventory-system/
What are the five purposes of inventory?
Learn the basics of inventory management, a crucial component of supply chain management. Understand how it supervises the flow of goods from manufacturers to warehouses to the point of sale. Discover the different stages goods go through in a business and how inventory management software helps track and manage this process.
Implementing Your Inventory System & How We Can Help -> https://asapsystems.com/blog/inventory-asset-tracking-blog0021/
What is the difference between inventory level and stock level?
While the terms “inventory” and “stock” are often used interchangeably, they have distinct meanings and implications within a business context. Understanding the differences between these two concepts is crucial for effective inventory management and financial reporting. The following table provides a clear breakdown of their key distinctions:
1- Inventory
- Definition: Encompasses all items held by a company: raw materials, work-in-progress goods, finished goods.
- Purpose:Used for production, cost calculation, and financial reporting.
- Management Frequency: Updated less frequently (quarterly or yearly for accounting purposes).
- Industry Relevance:Crucial for both distribution and production sectors.
- Valuation:Calculated using FIFO, LIFO, or weighted average methods.
- Additional Notes:Helps determine the sales price of the finished product (stock).
2- Stock
- Definition: Refers solely to finished goods that are ready for sale to customers.
- Purpose:Used to fulfill customer orders and directly generate revenue for the business.
- Management Frequency: Requires frequent updates, potentially multiple times a day, to reflect sales and demand.
- Industry Relevance:Primarily used in the distribution sector.
- Valuation:Determined by the current market price or the actual selling price to customers .
- Additional Notes:The value of stock directly impacts a business’s revenue.
Click here to get a full tour of our advanced inventory types -> https://asapsystems.com/products/inventory-system/advanced-inventory-types/
Barcode Inventory Tracking Software: Safeguard Your Inventory & Data with SOC2 Compliance & Advanced Security
Your institution’s inventory and the data that tracks it are valuable inventory. Our barcode inventory tracking software is built with a multi-layered approach, ensuring the highest levels of protection for your sensitive information and physical supplies. Our SOC2 compliance verifies our commitment to industry-leading security standards.
Key Security Features:
- SOC2 Compliance
- Data Minimization
- Robust Access Controls
- Encryption
- Secure Storage & Backups
- Comprehensive Security Training
- Incident Response & Breach Notification
- Regular Security Assessments
Learn More About Our User Security, Approval Cycles & Signature Capture aspects and how they can benefit your business -> https://asapsystems.com/products/inventory-system/system-features/user-security/
https://asapsystems.com/products/inventory-system/system-features/approval-cycles/
https://asapsystems.com/products/inventory-system/system-features/signature-capture/
Work in Process vs. Work in Progress: What's the Difference?
While often used interchangeably, work in process (WIP) and work in progress (WIP) have subtle distinctions in the business world.
1- Work in Process (WIP)
- Primarily used in production for goods undergoing a standardized production process.
- Timeframe: Refers to items expected to be completed quickly, often within a single accounting period.
- Examples: Partially assembled products like cars or electronics on a factory floor.
2- Work in Process (WIP)
- Used across various industries, including construction, software development, and creative fields.
- Timeframe: Encompasses long-term projects that may span multiple accounting periods.
- Examples: Buildings under construction, software in development, artistic works in progress.
3- Key Takeaway
The key difference lies in the project’s duration and complexity. WIP generally refers to short-term, standardized assembly processes, while WIP encompasses longer-term, often more complex projects across various industries.
Understanding this distinction is crucial for accurate financial reporting and inventory management. By classifying WIP and WIP correctly, businesses can better track their assets and make informed decisions about resource allocation and project timelines.
Click Here To Read More About The Tools Our Inventory System Offers -> https://asapsystems.com/blog/inventory-asset-tracking-blog0054/
Optimize Your Work-in-Progress (WIP) Inventory
Efficiently managing work in process (WIP) inventory is vital for manufacturers and other businesses alike. It’s about striking a balance between meeting customer demand and minimizing storage costs. Below, we’ve consolidated the best strategies to help you optimize your WIP inventory flow:
By implementing these strategies, all businesses can effectively manage their WIP inventory, reduce costs, improve efficiency, and enhance customer satisfaction. Remember, the key is to find the right balance between responsiveness to demand and minimizing excess inventory
The Cons of Not Having an Inventory System -> https://asapsystems.com/blog/inventory-asset-tracking-blog0025/
Less is More: The Lean Inventory Advantage
Lean inventory management is a strategic approach to minimizing waste and optimizing efficiency in the inventory process. It ensures that the right amount of stock is available at the right time for a smooth flow of goods. To achieve this, businesses adopt key principles:
Lean inventory management means always looking for ways to improve. Businesses regularly check their inventory to find and fix problems, get rid of delays, and cut down on waste. By doing so, they create a system that’s easier to manage and can adapt to changes, helping them make more money.
See How Our Inventory Management Saves You Money -> https://asapsystems.com/blog/inventory-asset-tracking-blog0016/
What Is Inventory Valuation?
Inventory valuation is the cornerstone of accurate financial reporting for businesses that deal with physical goods. It’s the accounting process of determining the monetary value of a company’s unsold inventory at a specific point in time, typically at the end of an accounting period.
By mastering inventory valuation, businesses can ensure accurate financial reporting, optimize profitability, and make informed decisions that drive long-term success.
Check out the 4 Ways We Can Balance Your Inventory Operations -> https://asapsystems.com/blog/inventory-asset-tracking-blog0002/
What is inventory revaluation?
Inventory revaluation is the process of adjusting the recorded cost of inventory to accurately reflect its current market value. This is essential for maintaining accurate financial statements and making informed business decisions.
1- Example
Imagine a company that sells high-end electronics. If a new model is released, the older models in their inventory may decrease in value. Inventory revaluation would involve adjusting the recorded cost of these older models to reflect their current market price.
2- Methods of Inventory Revaluation
There are several methods for conducting inventory revaluation:
- Inventory is recorded at either its original cost or its current market value, whichever is lower.
- Net Realizable Value (NRV): Inventory is valued at its estimated selling price, less any selling costs.
- Standard Cost: A predetermined cost is used for inventory and adjusted periodically to reflect market changes.
The specific method used depends on a company’s accounting policies and the nature of its inventory.
See The Inventory System How You Need It -> https://asapsystems.com/blog/inventory-asset-tracking-blog0065/
What's Triggering Your Next Inventory Revaluation?
Inventory revaluations are a crucial aspect of financial management, ensuring your business’s reported value aligns with market realities. There are several key triggers that signal it’s time to reassess your inventory’s worth:
1- Market-Related Triggers
- Supply Chain Disruptions: If events disrupt the availability or cost of your raw materials or ingredients, it’s essential to re-evaluate your inventory to reflect these changes accurately. This helps you make informed decisions about pricing and production.
- Demand Fluctuations: Sudden shifts in consumer preferences can significantly impact the value of your products. Revaluation ensures your financial reporting reflects the true market worth of your inventory.
- Market Price Changes: If the market price of your inventory increases or decreases significantly, revaluation ensures your financial statements remain accurate.
2- Internal Triggers
- Spoilage or Damage: If your inventory becomes damaged or expires, it’s necessary to revalue it to reflect its diminished worth. This allows you to make informed decisions about discounting or disposal.
- Changes in Production Output: If your production levels change, it’s important to reassess the allocation of fixed overhead costs to your inventory, ensuring accurate cost calculations and informed decision-making.
- Obsolete Inventory: Products that have become outdated or unsalable need to be revalued and potentially written off to avoid inflated asset values.
3- Financial and Regulatory Triggers
- Compliance with Accounting Standards: Regular revaluations are often necessary to comply with accounting standards and provide stakeholders with accurate financial information.
- Tax Implications: Inventory revaluations can impact on your taxable income and tax liability.
Remember, the frequency of inventory revaluations can vary depending on your industry, company size, and specific market conditions. Regularly assessing your inventory’s value is a proactive step towards maintaining financial transparency and making informed business decisions.
Check Out These 3 Tracking Tips To Consider During Doubt & Uncertainty -> https://asapsystems.com/blog/inventory-asset-tracking-blog150/
Conclusion
Thank you for diving into our comprehensive guide on inventory management systems.
As you’ve discovered, a robust inventory management system isn’t just a tool; it’s a strategic partner that streamlines operations, minimizes costs, and empowers data-driven decisions. By leveraging the insights gained from this guide, you can transform your inventory from a logistical challenge into a wellspring of profitability.
Remember, the journey doesn’t end here. The next step is to identify the ideal inventory management system that aligns with your specific needs and goals.
And that’s where we come in.
Designed with businesses like yours in mind, our Inventory Management System offers a comprehensive suite of features that simplify inventory tracking, forecasting, and optimization.
Take the leap and explore how we can revolutionize your inventory management. -> https://asapsystems.com/company/barcloud-contact-us/